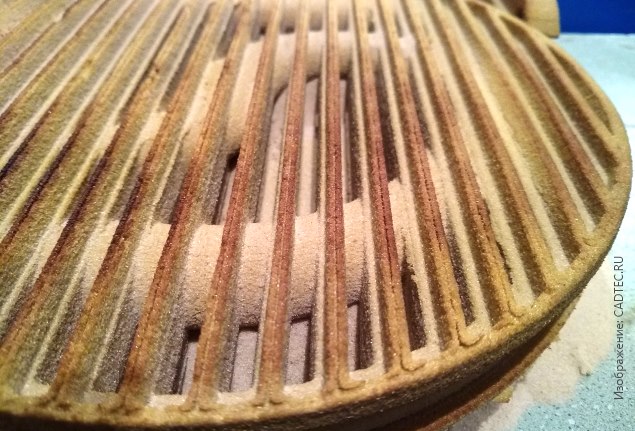
В машиностроении и металлургии сегодня предлагается много решений на базе аддитивных технологий – от печати полимерных прототипов и мастер-моделей до производства на 3D-принтерах промышленных металлических деталей.
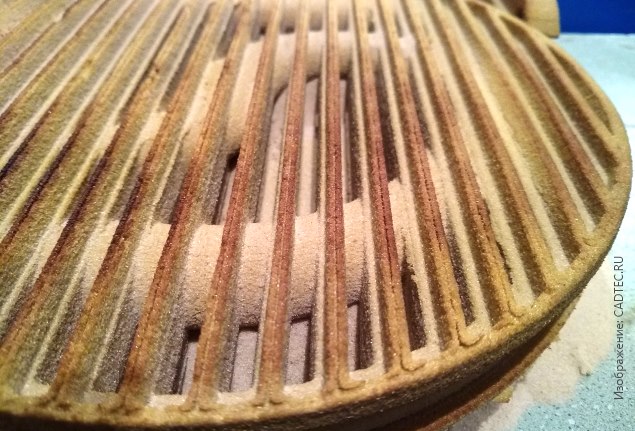
Рис. 1 Модель экономайзера, напечатанная на 3D-принтере
Традиционная технология получения форм для всех видов литья нуждается в изготовлении литейной оснастки. Это трудоемкий и дорогостоящий процесс, требующий высокой квалификации персонала и часто дорогостоящего оборудования, например станков с ЧПУ.
Создание сложной отливки на литейном производстве – весьма длительный процесс. К примеру, один из авторов материала во время работы на ОАО «Кузнецов» занимался изготовлением отливки опоры газотурбинного двигателя диаметром 1 400 мм, весом 475 кг. Процесс создания детали занял почти восемь месяцев. Большая часть времени была потрачена на получение и доводку литейной оснастки.
Технологии быстрого прототипирования позволяют значительно ускорить процесс изготовления литейной оснастки. Один из таких методов – 3D-печать песчано-полимерных литейных форм и стержней. 3D-принтер позволяет получать формы напрямую по данным компьютерной модели без использования промежуточной оснастки. Для печати форм используются кварцевый песок и смола.
Существуют две основные технологии создания форм на 3D-принтере – струйная печать (Binder Jetting) и селективное лазерное спекание (Selective Laser Sintering (SLS).
В первом варианте используется двухкомпонентное связующее – смола и отвердитель. Отвердитель смешивается с песком, формируется тонкий слой песчаной смеси, смола наносится с помощью печатающей головки в соответствии с формой сечения печатаемой модели. В местах нанесения смолы происходит химическая реакция, и песчаная смесь отверждается. Процесс послойного нанесения повторяется до полного построения модели.
СПРАВКА |
Рынок 3D-печати растет стремительными темпами. Если в 2017 году его объем превысил 7 млрд долларов, то к 2024 году, по оценкам экспертов, он достигнет отметки в 35,6 миллиарда [1]. Постоянно расширяется и сфера применения аддитивных технологий. В настоящее время 3D-печать наиболее активно применяется для создания прототипов. В перспективе будет возрастать доля производства готовой продукции или ее частей. Исследования показывают, что предприятия в ряде областей производства, освоившие технологии 3D-печати, получают явные преимущества. К тому же, по прогнозам Siemens, в течение пяти лет технологии 3D-печати подешевеют вдвое и станут в четыре раза быстрее [2]. |
При SLS-технологии применяется плакированный песок. Каждая песчинка покрыта слоем термореактивного полимера. На рабочий стол наносится слой песка, лазер нагревает поверхность в соответствии с геометрией сечения печатаемой модели, нагретый песок спекается. После окончания печати модели несвязанный песок удаляется. Напечатанная форма прокаливается в печи для достижения необходимой прочности.
На рисунке 2 показана печать сечения модели экономайзера на 3D-принтере производства CADTEC.RU. Лазерный луч «заливает» поверхность песка в соответствии с моделью сечения, нагретый песок спекается и приобретает начальную прочность. Далее деталь будет очищена от несвязанного песка и помещена в печь для прокалки, после чего форма будет готова к заливке.
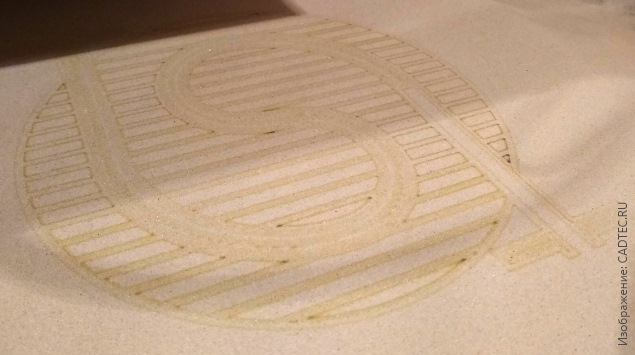
Рис. 2 Печать сечения модели экономайзера
В обоих случаях возможны частичная регенерация и повторное использование несвязанного песка.
Напечатанные формы применяются для изготовления отливок из алюминиевых и магниевых сплавов, сталей и чугунов. Технология 3D-печати обладает рядом преимуществ по сравнению с традиционными методами получения форм:
- Время, необходимое для разработки новой отливки по традиционной технологии, составляет от 2 до 6 месяцев, в некоторых случаях на это уходит до года. При использовании технологии 3D-печати песчаных форм процесс занимает всего 5-10 дней.
- Изготовление форм сложной геометрии по традиционной технологии имеет свои ограничения, а в отдельных случаях крайне затруднительно или вообще невозможно. 3D-печать позволяет получать формы и стержни практически неограниченной сложности, отпадает необходимость в применении формовочных уклонов.
- В процессе отработки технологии для литейного производства приходится многократно менять геометрию отливки, а значит, и формы, корректировать литниково-питающую систему. Для каждого варианта нужно изготовить соответствующую оснастку. Это приводит к существенному удорожанию производства отливок, особенно мелкосерийных или единичных, и значительно затягивает процесс по времени. В случае изготовления форм на 3D-принтере достаточно откорректировать компьютерную модель формы и распечатать ее заново. Цифровые технологии производства обеспечивают низкую стоимость копирования.
Печать форм на 3D-принтере схожа с изготовлением форм и стержней по методу ХТС (холодно-твердеющие смеси или Cold Box) – в обоих случаях используются аналогичные материалы. Важно, что аддитивные технологии позволяют не только изготавливать опытные образцы, но и отрабатывать технологию литья изделий для серийного производства, т. к. теплопроводность, прочность, газопроницаемость песчаных форм, изготовленных на 3D-принтере, такая же, как у стандартных песчаных форм и стержней, которые будут изготавливаться при серийном производстве.
Полагаем, что применение технологии 3D-печати песчаных форм позволит кардинально сократить сроки изготовления отливки опоры газотурбинного двигателя, рассмотренной выше, и значительно снизить стоимость готового изделия.
Иные варианты использования аддитивных технологий в литейной промышленности
Кроме получения форм на 3D-принтере распространена печать мастер-моделей из пластика, воска, полистирола и других материалов. Пластиковые модели могут применяться для получения обычных ХТС песчаных форм не сложной геометрии.
Восковые и полистирольные модели будущей отливки изготавливается методом 3D-печати, затем на модель послойно наносится керамическое покрытие, так формируется литейная форма.
В случае использования воска мастер-модель растапливается и удаляется из формы перед литьем, остается пустая керамическая оболочка – технология литья по выплавляемым моделям. При использовании полистирольных моделей заливка металла производится в форму с моделью, которая сгорает в процессе – технология литья по выжигаемым моделям.
Если раньше для изготовления восковых моделей применялись только специальные 3D-принтеры для печати воском, то сейчас появились материалы на основе модельного воска, выпускаемые в катушках для использования в обычных FDM (пластиковых) 3D-принтерах.
Альтернативой литью является прямое изготовление металлических изделий на 3D-принтере. Этому способствует развитие технологий 3D-печати металлическими порошками; появление стандартов и накопление информации о характеристиках получаемых изделий; снижение стоимости оборудования и, что очень важно, снижение цены и увеличение доступности расходных материалов – металлических порошков.
Опыт разработки и использования песчаных 3D-принтеров
Несмотря на явные преимущества, технология 3D-печати форм мало применяется в отечественной промышленности. Барьерами для проникновения являются высокая цена оборудования и стоимость его эксплуатации, низкая доступность расходных материалов, недостаток сотрудников необходимой квалификации.
Востребованность технологии со стороны производства и накопленные компетенции, необходимые для ее инженерного воплощения, стали основой для запуска проекта по разработке собственного оборудования для 3D-печати песчано-полимерных литейных форм. Наша компания «Центр аддитивных технологий» разработала 3D-принтер, который «выращивает» песчаные литейные формы слой за слоем непосредственно по компьютерной модели.
В процессе НИОКР были опробованы струйная и лазерная технологии 3D-печати песчаных форм. Каждая показала свои преимущества и недостатки, но формы, полученные с их помощью, имели сопоставимые характеристики. В настоящее время продолжается работа над 3D-принтерами на базе технологии селективного лазерного спекания.
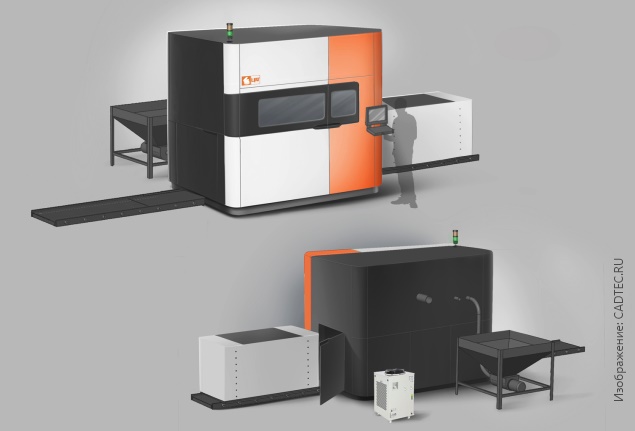
Рис. 3 Разработка промышленного дизайна мелкосерийной модели 3D-принтера
Для печати используется кварцевый песок мелкой фракции от 100 мкм. Он покрывается новолачной смолой со специальными присадками. Использование доступных расходных материалов позволяет добиться низкой стоимости и снизить цену конечных изделий. Точность изготовления форм – 0,25-0,5 мм, максимальные габариты форм составляют 1800 x 1000 x 700 мм.
Заказчикам часто требуется изготовление форм и стержней или готовых отливок. Как правило, необходимо изготовить одну или несколько форм. Для большого числа изделий 3D-печать остается достаточно дорогим способом изготовления и по стоимости проигрывает серийной оснастке. Для небольших серий требуется оценка экономической составляющей. 3D-печать может оказаться выгоднее, особенно при возникновении необходимости изменения конструкции изделия в процессе работы.
Для единичных отливок и небольших партий изделий форма и стержни могут быть полностью напечатаны на 3D-принтере. В случае партии большего объема могут использоваться стержни, изготовленные на 3D-принтере, а форма – традиционная песчаная. При серийном производстве сложные стержни, напечатанные на 3D-принтере, могут использоваться в серийной кокильной оснастке.
Общие затраты определяет расход материала (машинного времени) и объем подготовительных работ. Заказчик может предоставить 3D-модель будущей формы, 3D-модель изделия или просто чертеж. Также необходимо знать число изделий и материал будущих отливок.
Хороший конструктор по компьютерной модели детали за день готовит 3D-модель формы с необходимыми припусками под механическую обработку и спроектирует ЛПС. Еще день-два уходят на печать формы на 3D-принтере. Практика показывает, что самым долгим этапом оказывается процесс изготовления готовых отливок. Из-за отсутствия собственного литейного производства приходится ждать, когда партнеры будут лить подходящий материал.
Часто необходимо изготовить пресс-форму для литья пластиковых или резиновых изделий. С помощью 3D-печати можно создать песчаную форму для элементов пресс-формы. При литье в песчаные формы невозможно сразу обеспечить требуемую точность изготовления и качество поверхности пресс-форм. Получаемые заготовки необходимо доработать на станке с ЧПУ. При таком подходе существенно сокращается время обработки, и, соответственно, себестоимость по сравнению с вытачиванием из цельного куска материала.
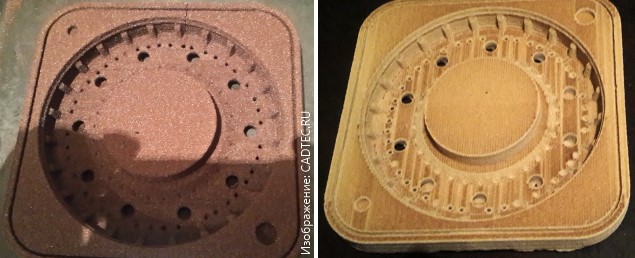
Рис. 4 Полуформа, напечатанная на 3D-принтере, до и после прокалки
Использование 3D-принтера собственной разработки позволяет в десять и более раз ускорить процесс изготовления новых отливок для машиностроительных предприятий.
И. А. Адушев, генеральный директор, Л. П. Павлов, исполнительный директор,
ООО «Центр аддитивных технологий», г. Самара
Список литературы:
- Wohlers Report 2019
- Pictures of the Future. Siemens
- Адушев И. А., Павлов Л. П. Применение аддитивных
технологий для получения песчано-полимерных форм//
Литейное производство. 2016 №6, с.36-40